Une des grandes originalités du programme
Ariane 5 est la réalisation in situ d' un élément majeur du lanceur, les
boosters EAP compte tenu des difficultés techniques et économiques liés au
transport Europe Guyane des segments du propulseur chargé de poudre.
Un accord signé en avril 1988 confie la fabrication du segment avant S1 à l'
Italie dans l' usine de Collefero par SNIA BDP (depuis devenu Fiat Avio). Les
deux autres segments, central et arrière S2 et S3 devant donc être coulé en
Guyane. Ces derniers reçoivent leur propergol solide à l' UPG Usine de
Propergol Guyane, à 6 km au sud du site de lancement et 1 km au Sud-Est du
bâtiment d'intégration des boosters BIP et 1 km à l'Est du banc d'essai statique
BEAP. Les segments intermédiaire et arrière réalisées en Allemagne par MAN
Technologie sont amené vide en Guyane pour être remplis de 200 tonnes de
propergols.
L' usine en service depuis 1991 est un vaste complexe de 40 bâtiments occupant
une surface de 300 hectares et comporte deux malaxeurs de 6800 tonnes de
capacité et un puit de coulé. Sa capacité annuelle est de 3000 tonnes, assez
pour remplir 32 segments EAP, pour 8 lanceurs par an.
Le segment avant S1 plus petit est rempli de propergol en Italie à Colleferro
et livré directement en Guyane pour intégration.
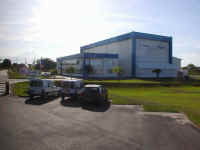
L'entrée de la zone UPG au Sud
des ELA. On y accède par la route de l'espace soit par le centre spatial au
poste Orchidé, soit par la route piste Corneille juste avant la station
météo. A droite le bâtiment d'EADS.

La zone UPG vue par le Sud Est et
par le Nord
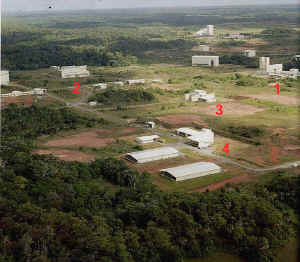
|
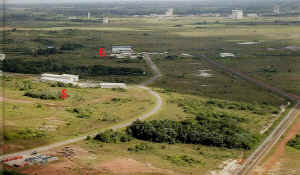 |
1- atelier de
préparation des structures
2- bâtiment de contrôle non destructif
3- mélangeur 1
4- préparation propergol.
5- atelier de maintenance
6- zone administrative (entrée) |
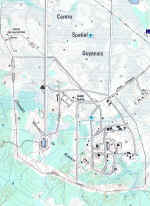
L'usine de propergol de Guyane (UPG) est
dédiée à la fabrication, au contrôle et au stockage des chargements des
segments central et arrière des EAP, chaque segment mesurant environ 11
mètres de long et 3 mètres de diamètre et comptant 105 tonnes environ de
propergol solide.
Le stockage et le contrôle du segment avant,
qui contient 24 tonnes de propergol, sont également effectués à l'UPG, à son arrivée d'Europe.
Trois zones composent l'usine:
_ Une zone administrative au Nord
_ Une zone inerte
_ Une zone pyrotechnique
L'UPG comprend toutes les installations
nécessaires à la fabrication de manière autonome, des chargements des
segments. Ces installations permettent de remplir les fonctions
suivantes:
_ Stockage et mise en oeuvre de matières premières
_ Préparation des segments à leur arrivée d'Europe avec mise en place d'un
revêtement de liner sur les protections thermiques internes
_ Mise en oeuvre du propergol (réalisation du liant et malaxeur)
_ Contrôle des matières premières et des matériaux
_ Réalisation du chargement comprenant la coulée, le moulage, la cuisson du
propergol
_ Contrôle non destructif des segments chargés
_ Manutention, transport, entretien, maintenance, sécurité, intervention de
secours
_ Conduite centralisée des opérations et saisie des données.
La construction démarre en juillet 1988 avec
le déblaiement du site. La réalisation nécessite un million de mètres cubes de
terrassement, 9000 mètres cube de béton et 3000 t de structures métalliques.
Les réseaux de circulation comportent 18 km de voies. Le bâtiment le plus haut
(préparation des segments) comporte deux tours de 40 m. Trois puits capables de
recevoir les segments du P230 ont été creusés dont 2 mesurent 10 m de
diamètre et 25 m de profondeur (puits de coulée).
En 2001, un second bâtiment équipé d'une
installation de coulée-cuisson et capable à terme de recevoir une seconde
installation (pour un objectif de cadence : 10 lancements par an) est construite
par la société Technips qui avait déjà réalisé les premiers puits..
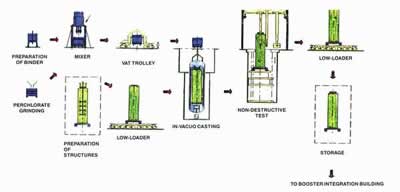
Systèmes principaux :
_ Matières premières: perchlorate d'ammonium, aluminium en poudre, polymère
PBHT, plastifiant DOZ, un laboratoire de contrôle physico-chimique des
matières.
_ Manutention segments à l'arrivée
_ Préparation des segments avant chargement
_ Mise en oeuvre du propergol: 5 ateliers:
_ Une unité de préparation du liant du propergol
_ 2 ateliers de mise en œuvre du propergol
_ Un atelier de malaxage du propergol
_ Un atelier de nettoyage des cuves du malaxeur
_ Contrôle des matériaux mis en oeuvre
_ Chargement des segments
_ Contrôle non destructif: ultrasons, endoscopie, rayons X
_ Stockage
_ Poste de commande centralisé
_ Zone de maintenance
_ Zone administrative
_ Moens de transport mobiles
Sous-systèmes :
_ Energie électrique
_ Climatisation
_ Voirie
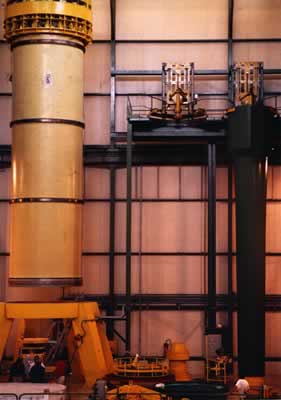
Outillage découpe
manchette et la zone de stockage des 2 noyaux
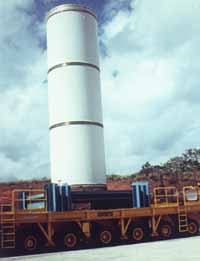
Transfert intérieur sur un fardier du Corps
du Propulseur Préparé (CPP)
ATELIER DE PREPARATION DES STRUCTURES
Dans ce bâtiment de 1900 mètres carré, les segments vides subissent les opérations suivantes:
_
Démontage des outillages de transport et montage des outillages de fabrication
_ Etuvages des segments (assainissement des protections thermiques,
pré-chauffage avant enduction de liner)
_ Pulvérisation de solvant sur les
protections thermiques des segments pour avivage
_ Revêtement des protections
thermiques par une couche de liner pulvérisé
_ Contrôle par un moyen vidéo
de l'intérieur des segments avant et après enduction de liner
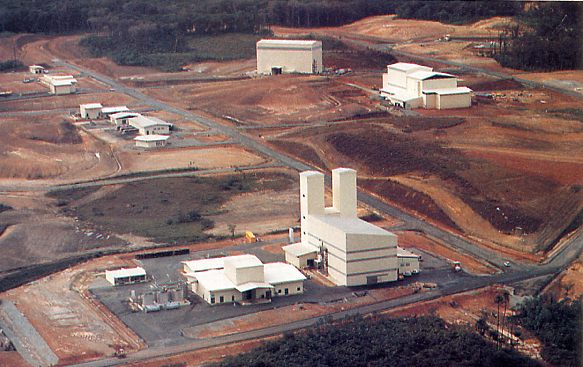
Le bâtiment de préparation des
structures au premier plan. Au fond le puit de coulée et à droite le bâtiment
de contrôle non destructif.
Le déplacement des segments entre les divers postes se fait en vertical sur
palettes à coussins d'air. Le segment enduit de liner est ensuite transféré
à l'atelier de coulée.
Les systèmes principaux sont :
_ Poste de montage des outillages comprenant:
_ 1
élévateur à structures de capacité 120 kN
_ 1 machine élévatrice de mise
en place des outillages partie basse
_ 1 poutre roulante et 1 palonnier de
préhension pour outillages partie haute
_ 2 étuves
_ Machine d'aspersion solvant MEC
_ La machine liner comprend:
_ 1 perche rigide
_ La motorisation en rotation
de la perche
_ 1 plateforme mobile le long de la perche support de la cuve de
liner, du pistolet, de la pompe d'asperstion et du système vidéo pour le
contrôle de l'intérieur du segment
_ Palettes à coussin d'air
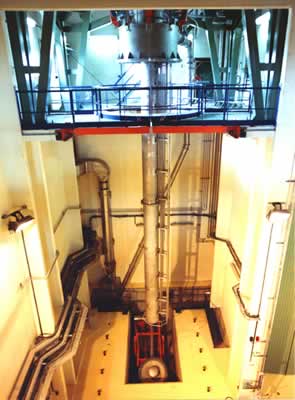
Machine à enduction du liner
MALAXAGE PROPERGOL 1800 GALLONS
Deux ateliers identiques existent pour
préparer le propergol. Chaque atelier a pour fonction de réaliser 12000 kg de
propergol dans une cuve spécifique en ajoutant du liant déjà préparé et en
mélangeant le perchlorate d'ammonium, le réticulant et les catalyseurs de
polymérisation. Les diverses opérations se font en température contrôlée,
à pression atmosphérique ou sous vide.
Systèmes principaux :
_ 1 bâti support
_ 1 cuve de 7000 litres mobile sur rails
_ 1 tête de malaxage à 3 pales entraînées électriquement
_ Des dispositifs d'introduction à distance des charges pulvérulentes et des
ingrédients liquides
Sous-systèmes : Alimentation électrique,
pompes à vide, groupe de chauffage, refroidissement, air comprimé,
climatisation, palans de manutention des conteneurs de matières, détection
d'incendie-noyade. Contrôle-commande automatique.
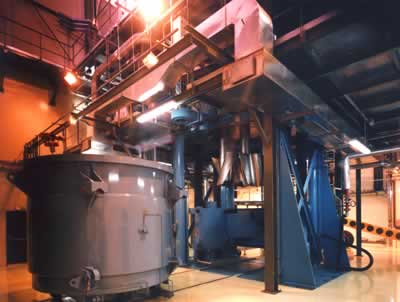
Malaxeur
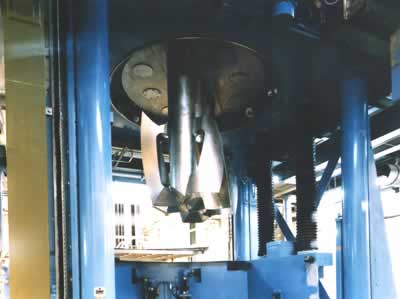
Pales du malaxeur
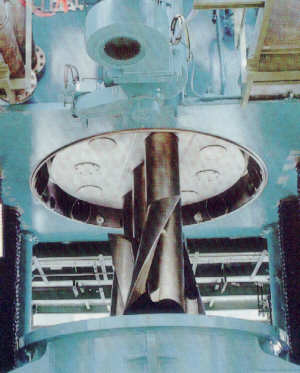
Le mélangeur
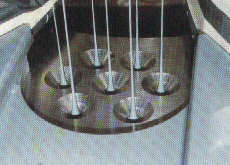
ATELIER DE COULEE
Cet atelier (bâtiment 303) dans lequel sont chargés les segments comporte 2 puits
de 5 m de diamètre et 19 m de hauteur équipés
d'une enceinte chauffante thermostatée à double enveloppe et panneaux radiants
dans laquelle est placé le segment. Le segment est positionné dans le puits à
l'aide d'un pont roulant de 2000 kN muni d'un palonnier automatique. Le segment
est équipé avec des outillages de moulage tels que le noyau central (15t, longueur 12m et diamètre 1,2 à 2m). Le
propergol pâteux provenant de la cuve de malaxeur positionnée au-dessus du
puits à l'aide de rails est coulé par gravité dans le segment. Le propergol
polymérise ensuite pendant plusieurs jours à température constante dans
l'enceinte à pression atmosphérique. Les outillages de moulage sont ensuite
extraits du pont roulant, le segment est positionné sur un bâti de 200 t pour
découpe de finition et pesée, équipé des outillages de stockage, puis placé
sur la palette à coussin d'air solidaire du fardier automoteur
Les systèmes principaux sont:
_ 2 puits de coulée
_ 1 bâti automatique de découpe
de la protection thermique pour finition du chargement
_ 1 table élévatrice
pour outillages sous bâti
_ 2 postes d'étuvage des outillages (poinçons)
_ 2
postes de stockage à la verticale des noyaux
_ 1 poste de nettoyage des noyaux
(plate forme mobile)
Un second bâtiment (304) est en construction
à coté mètres de distance avec deux puits également dont un seul sera en
service pour l' instant afin d' augmenter la cadence de production de 8 tirs par
an. Il sera opérationnel en 2004.
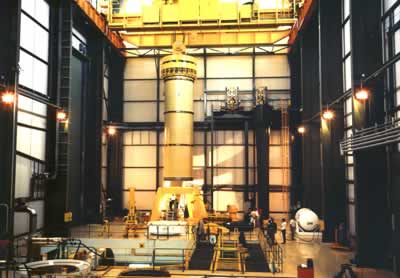
Puit de coulée
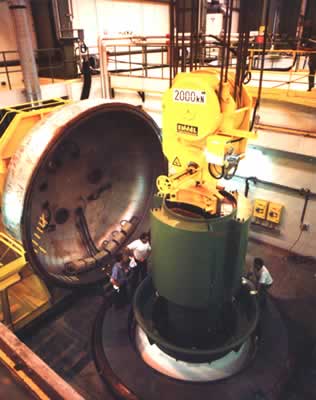 |
Mise en place du noyau dans
puits de coulée et vue de dessus
du dôme du segment n° 3, le couvercle du puits sera bientôt fermé pour
assurer la cuisson du propergol pendant 10 jours. Dix cuves sont nécessaires
pour remplir un segment
|
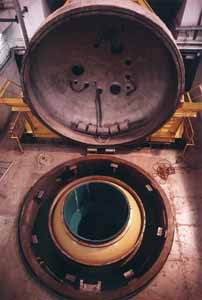 |
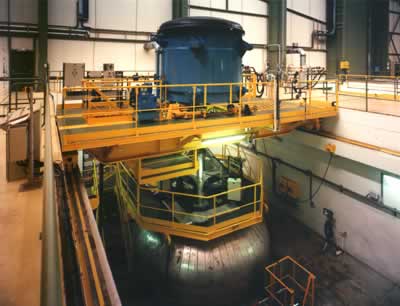
Coulée
Banc de démoulage et de découpe
de l'arrière du segment S3
CONTROLE NON DESTRUCTIF
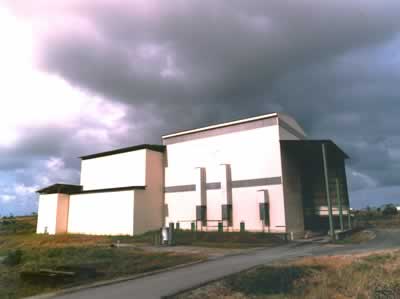
Dans ce bâtiment, spécialement conçu pour
protéger les opérateurs ainsi que l'environnement des rayonnements ionisants,
sont effectués les contrôles non destructifs des segments après coulée.
Systèmes principaux :
_ Un hall dans lequel se trouve un dock élévateur de 2000 kN pour montage et
démontage d'outillages.
_ Un poste d'endoscopie qui consiste en un
équipement vidéoscopique capable d'explorer les 11m du canal central du
chargement et d'y faire de la métrologie tridimensionnelle.
_ Un poste de contrôle automatique par
ultrason de la face supérieur des segments chargés.
_ Un site de radioscopie télévisée à
rayons X avec un plateau tournant élévateur de 2000 kN permettant de déplacer
le segment devant le générateur RX.
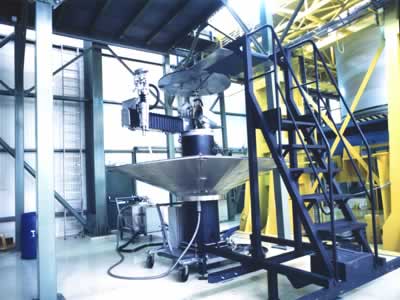
Ultra-sons
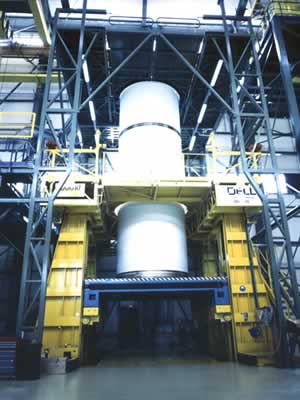
Endoscopie
Rayons X
BATIMENTS DE STOCKAGE EAP
Le bâtiment 313 et 314 sert au stockage des
boosters. Le bâtiment 315 livré en mai 1999 permet de stocker 8 boosters
complets avant le transfert au BIP.
|